

After the order is completed by a technician, it’s closed out and the data is entered into the system, making it available for reports and planning.Ī mobile CMMS can streamline this entire maintenance process by allowing technicians to access and update work order information on site, saving valuable labor hours by keeping travel times to a minimum.
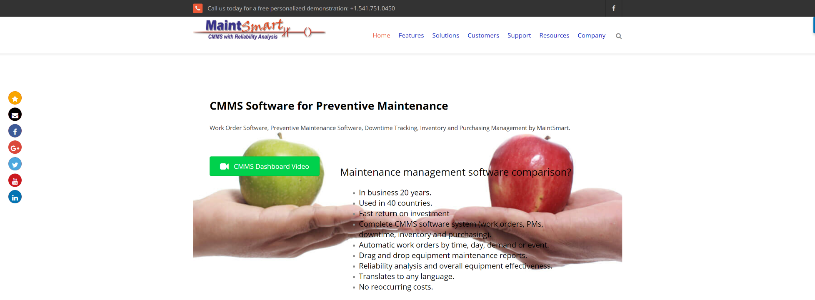
Some systems can even automatically generate orders based on data from sensors. Additionally, recurring orders may be created to handle preventive maintenance and inspections.
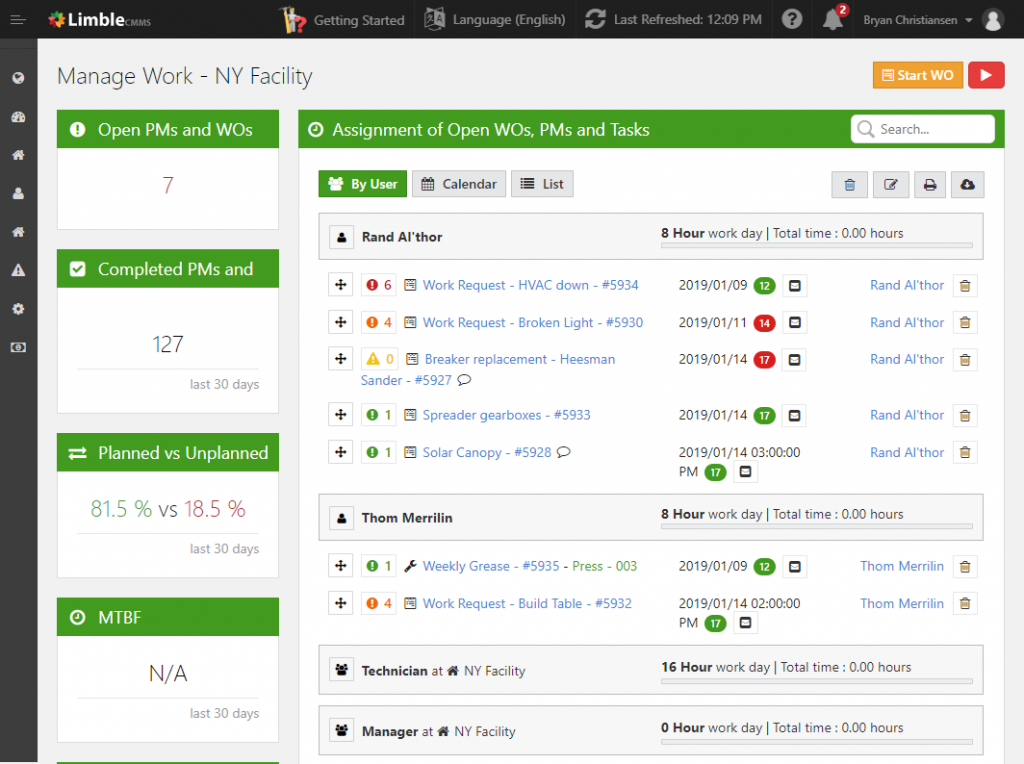
This data is then processed into reports used by maintenance managers and other departmental heads to make data-driven decisions.Īny time a work request is submitted, maintenance teams use a CMMS to create an order. Work orders contain key asset maintenance data including parts and costs, wrench time, asset repaired, and time to complete. When an order is closed, the data is processed by the system. Modern systems even operate on multiple platforms, from desktop PCs to handheld tablets and smartphones, making them a powerful way to streamline maintenance processes.Īt a high level, computerized maintenance management software is a data-driven solution, and the work order feeds that data. With a CMMS system, teams can easily record and organize asset data, plan preventive maintenance tasks, create work orders, and generate reports. CMMS software improves asset management by eliminating the need for manual spreadsheets and consolidating all maintenance team activities in one place. A computerized maintenance management system (CMMS), also referred to as maintenance management software or asset management software, is software that stores data about maintenance operations, such as maintenance performed on equipment, machinery, and other assets.
